Details
Place of Origin: | Ningbo China | Condition: | New |
Type: | Machining Parts | Spare Parts Type: | SIM Slot |
Video outgoing-inspection: | Provided | Machinery Test Report: | Provided |
Marketing Type: | Ordinary Product | Material: | Stainless Steel |
Plating: | Chrome | Warranty: | 1 Year |
Key Selling Points: | Long Service Life | Weight (KG): | 0.02 KG |
Applicable Industries: | Garment Shops, Construction works | Material Capabilities: | Stainless Steel, cemented carbide, iron-based, tungsten alloy |
Weight: | 0.5~240g | Color: | various |
Shape: | custom | Tolerance: | 0.03~0.05 mm |
After-sales Service Provided: | Online support | After Warranty Service: | Online support |

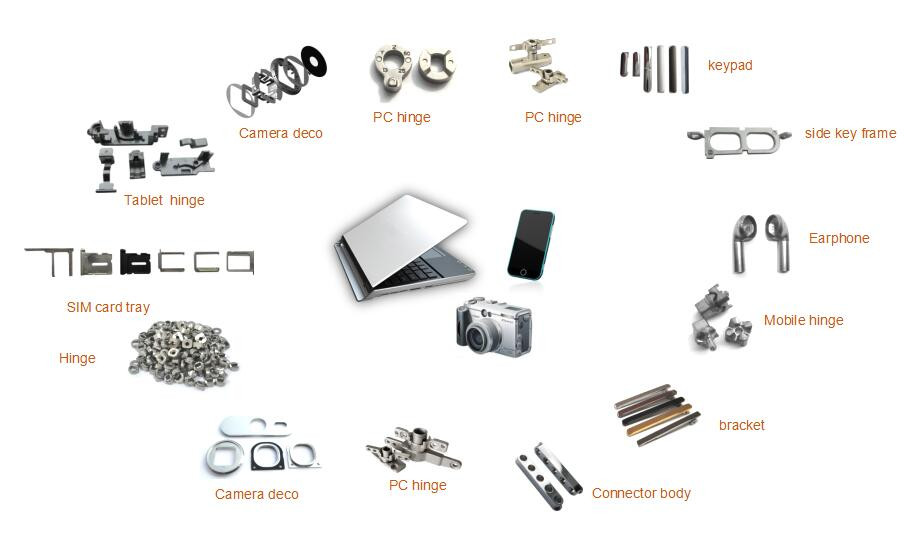
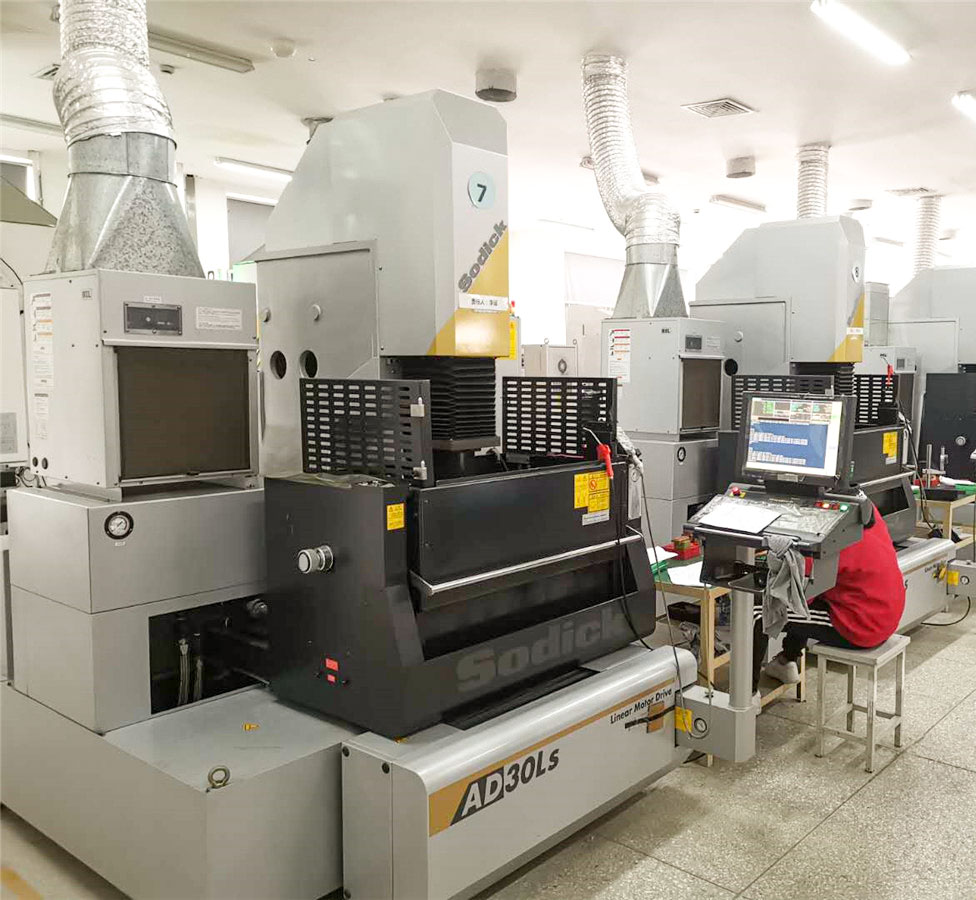
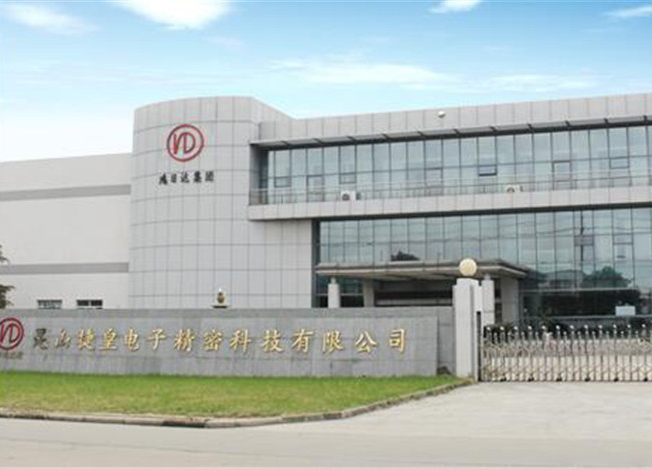
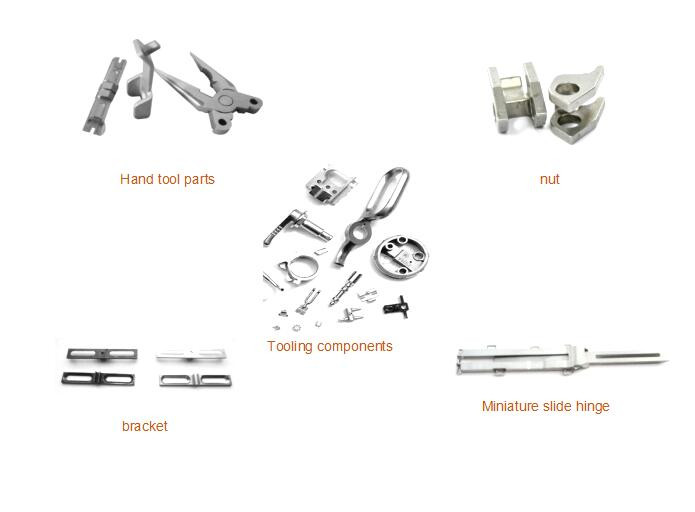
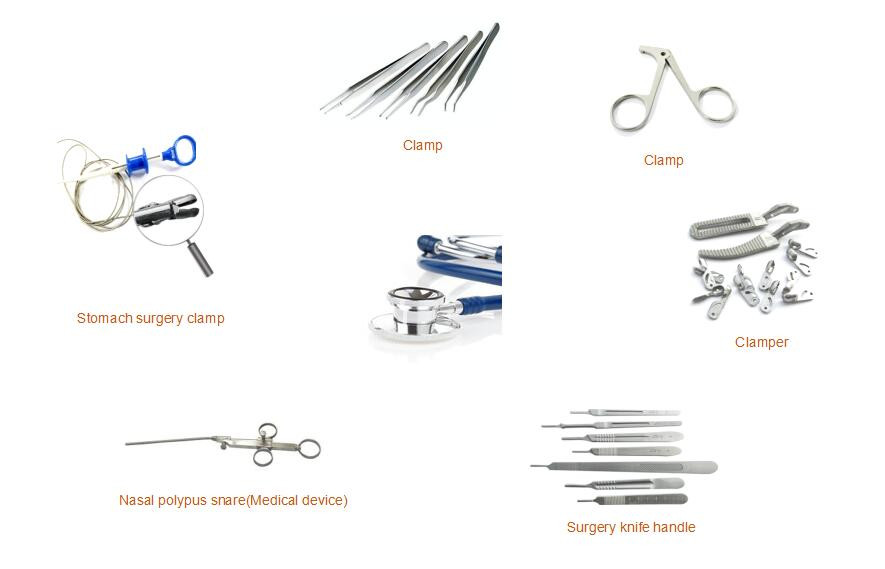
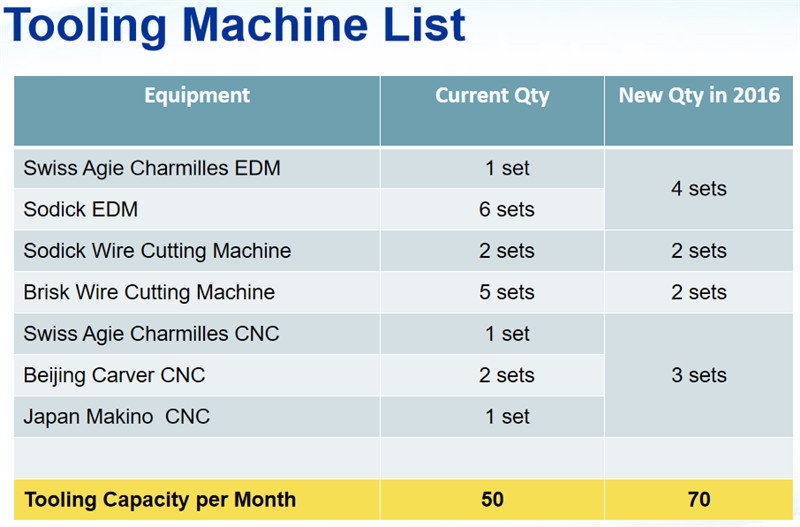

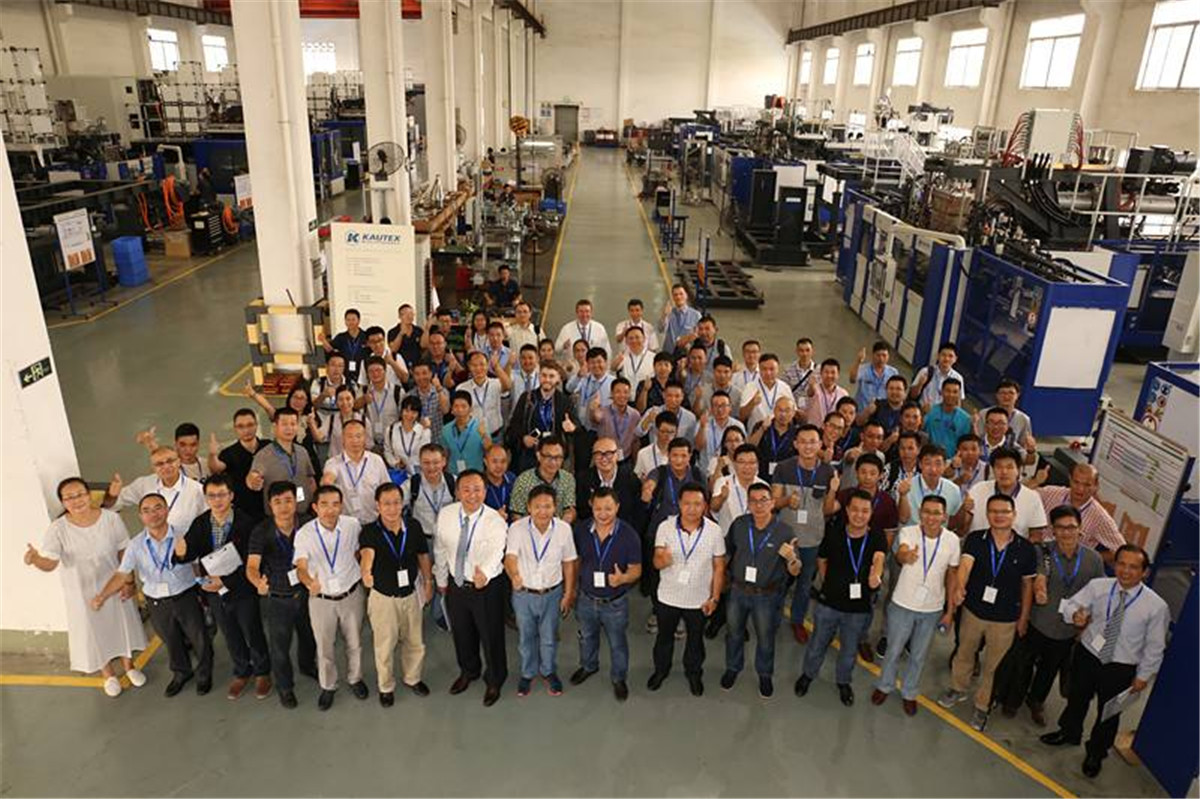
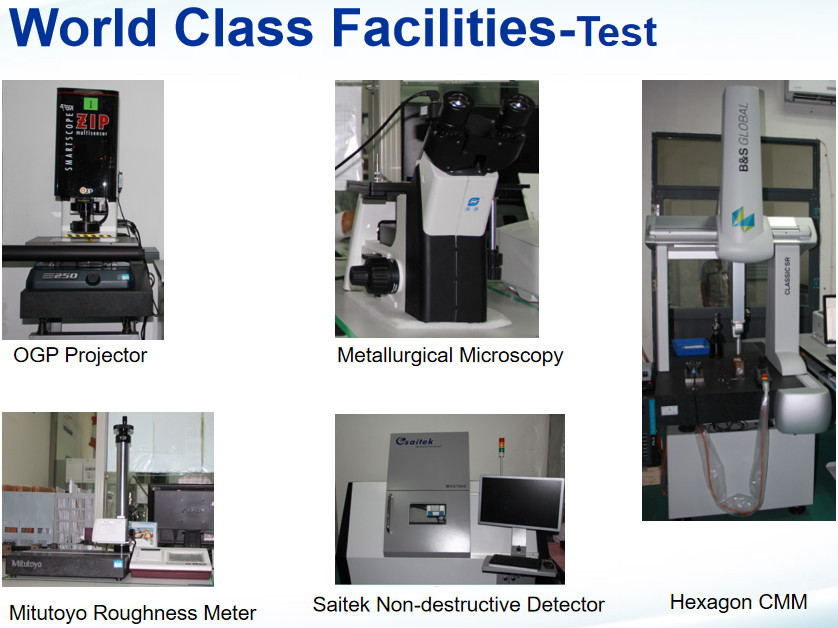
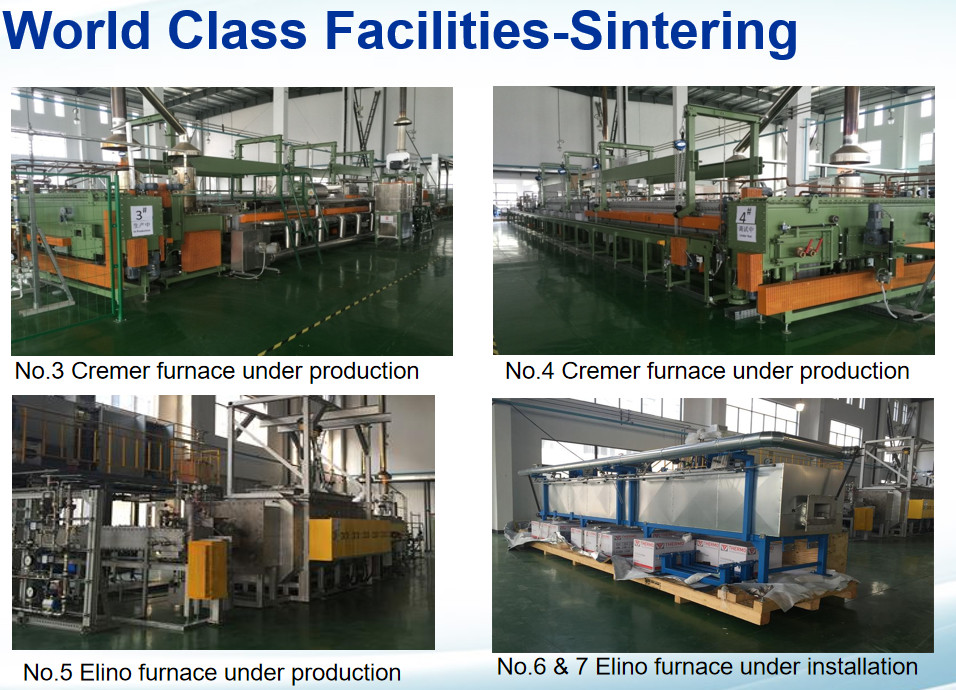
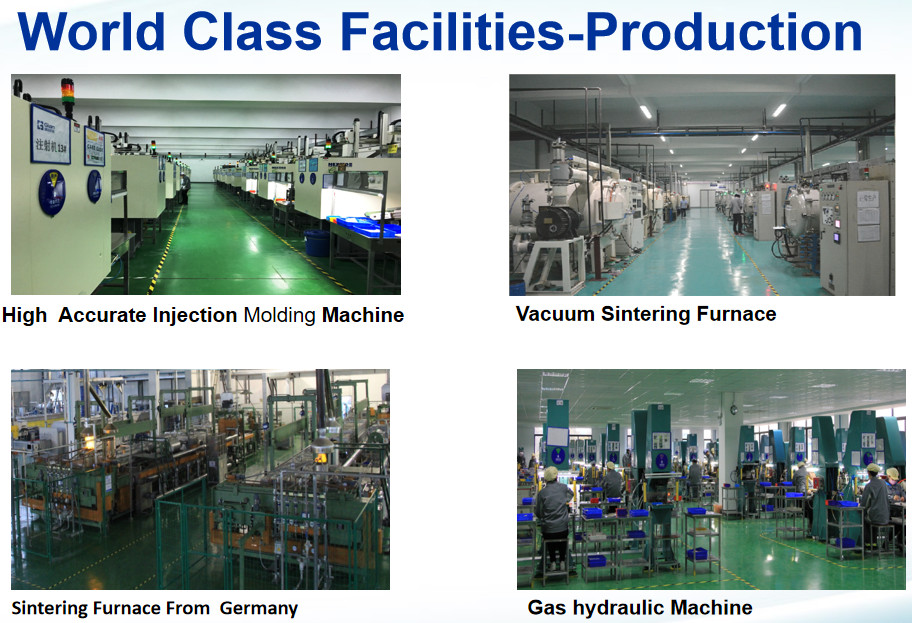
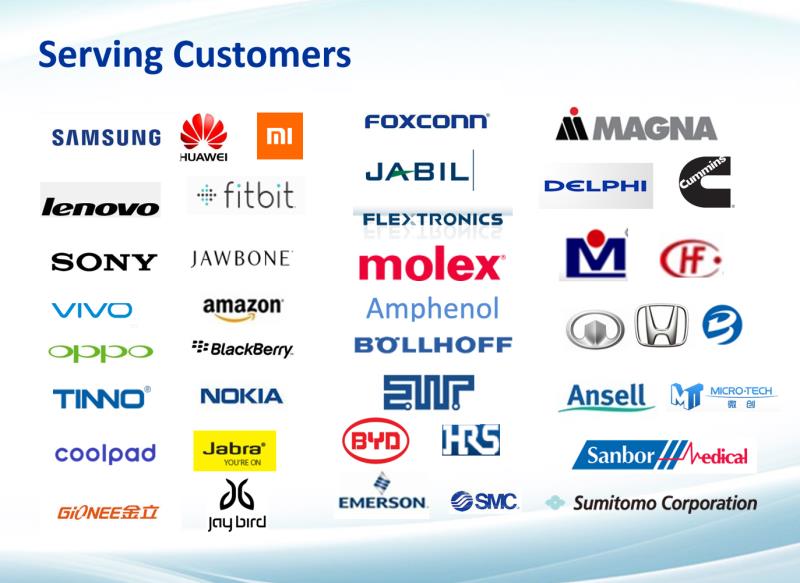