Details
Brand name | OEM & ODM |
Product type | MIM Powder Metallurgy Military Parts |
Material | Stainless steel 316L 304 17-4PH peptide Fe2Ni Fe4Ni Fe8Ni |
Post-Sintering | Polishing,Wire-drawing,Sandblasting,Plating,Coated,etc. |
Size | Custom |
Tolerance | 10mm±(0.02-0.04)mm |
Forming Method | Powder Injection Molding |
Sintering method | Solid phase sintering |
Sintering environment | Vacuum |
Mold material | Stainless steel |
Application | Military parts |
Shape | Custom |
OEM | Accept |
QC system | 100% inspection before shipment |
Payment terms | T/T at sight, Paypal, Western Union,etc. |
Lead time | 7-15 working days |
Supply capability | 500000 Piece Per Month |
Packaging | PP bag / Anti-static film / anti-static plastic disc |
How does MIM work ?
MIM is the process which merges plastic injection molding and powdered metallurgy. It offers greater design freedom and a manufacturing capability of producing precise, complex parts in large quantities.
Contrast for MIM and Precision Casting Molding
Property | MIM | Precision Casting Molding |
Minimum Thickness | 0.4mm | 2mm |
Maximum Thickness | 10mm | Unlimited |
Minimum Diameter | 0.4mm | 2mm |
Tolerance of Diameter 4mm | +/-0.06mm | +/-0.2mm |
Surface Roughness | 1μm | 1μm |
Application areas for injection molding
MIM--Accessories The Headset Accessories Flight Instrument Equipment Parts Smart Wearable Device Parts Machinery And Equipment Parts 1.When can I get the price and what do I need offer? Quotation will be provided within 24 hours after we receive full production(you need offer 2D and 3D of products)information.If the quotation is urgently,please tell us,we will speed up it. 2 What is the production cycle of MlM? For samples,it is about 20-25 calendar days and for goods,it is about 5-7 calendar days for the first batch. 3 What material can you produce? We can produce iron,stainless steel,ceramics,tungsten steel parts. 4.Why should I choose MlM. The advantages of MIM is that it can produce high precision complex parts,which are difficult to be produced by traditional technologies,such as CNC or casting.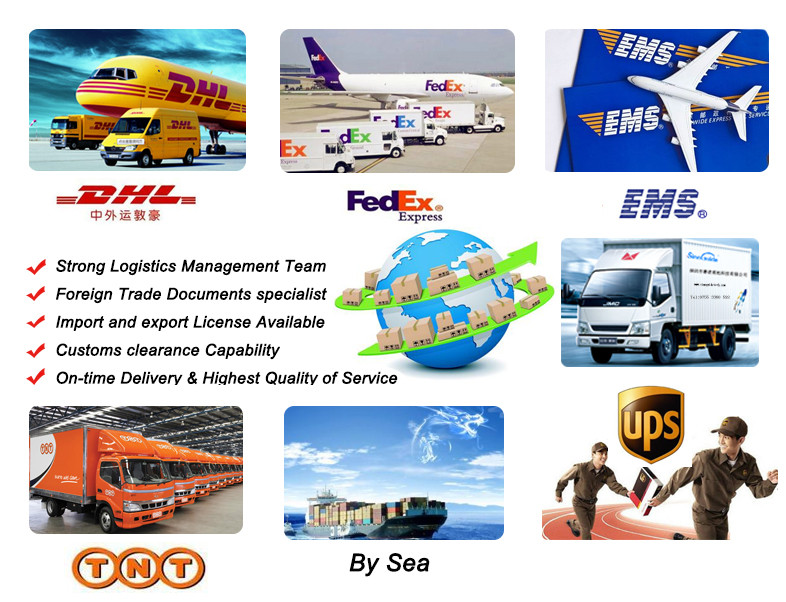
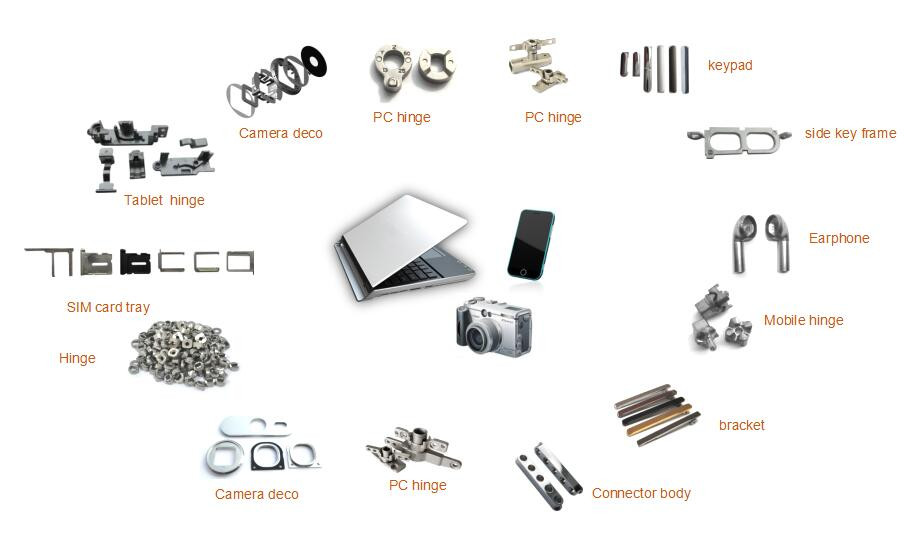
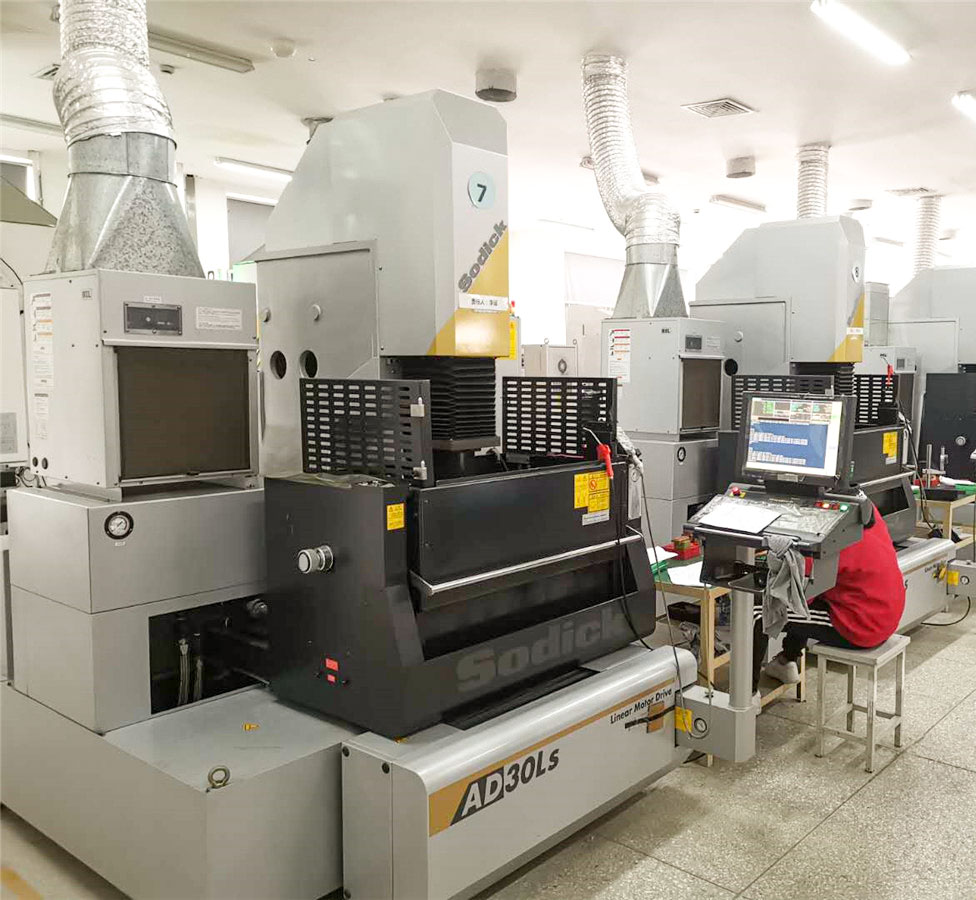
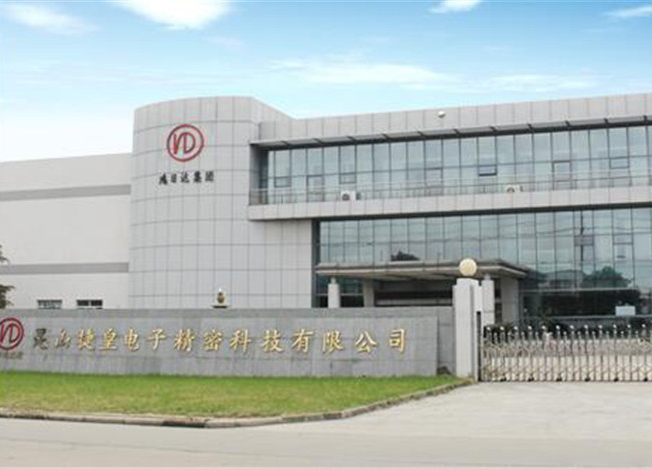
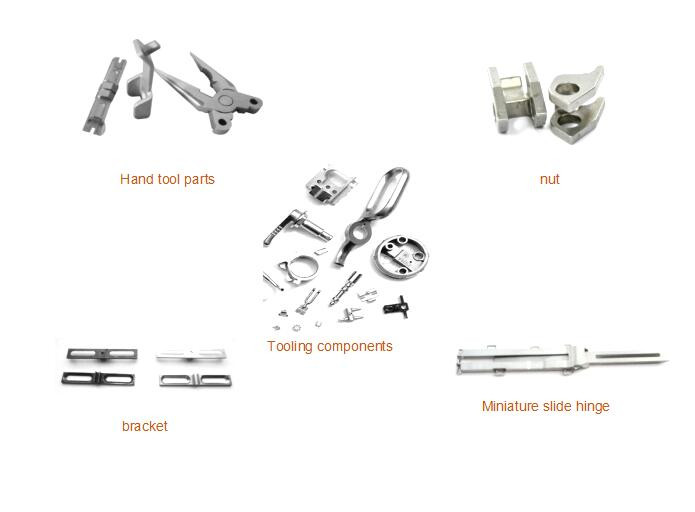
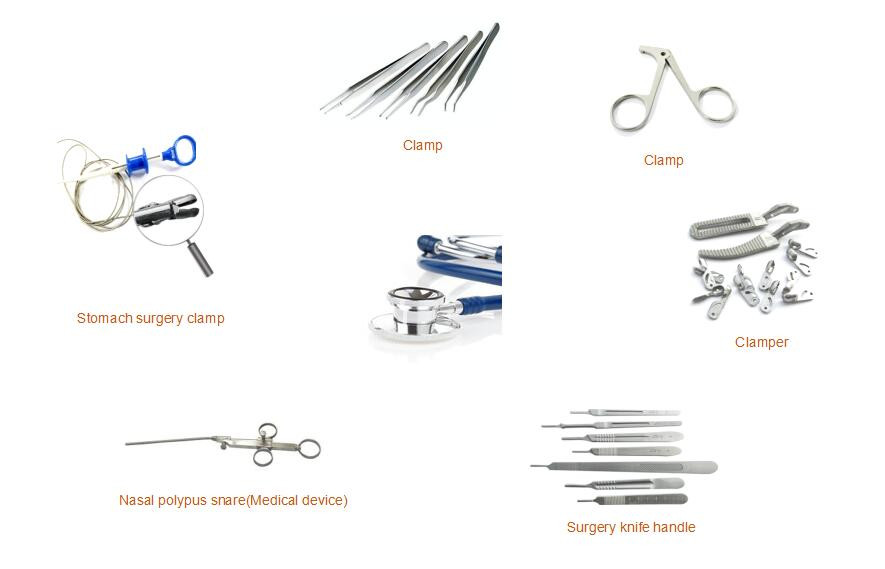
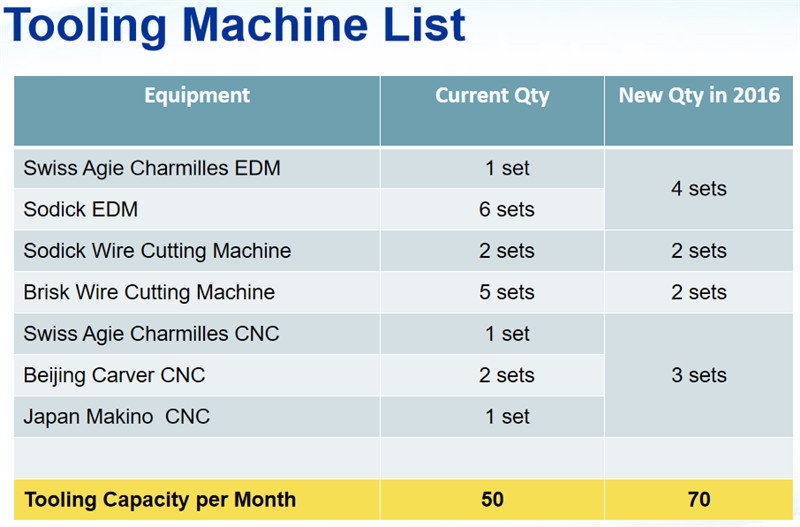

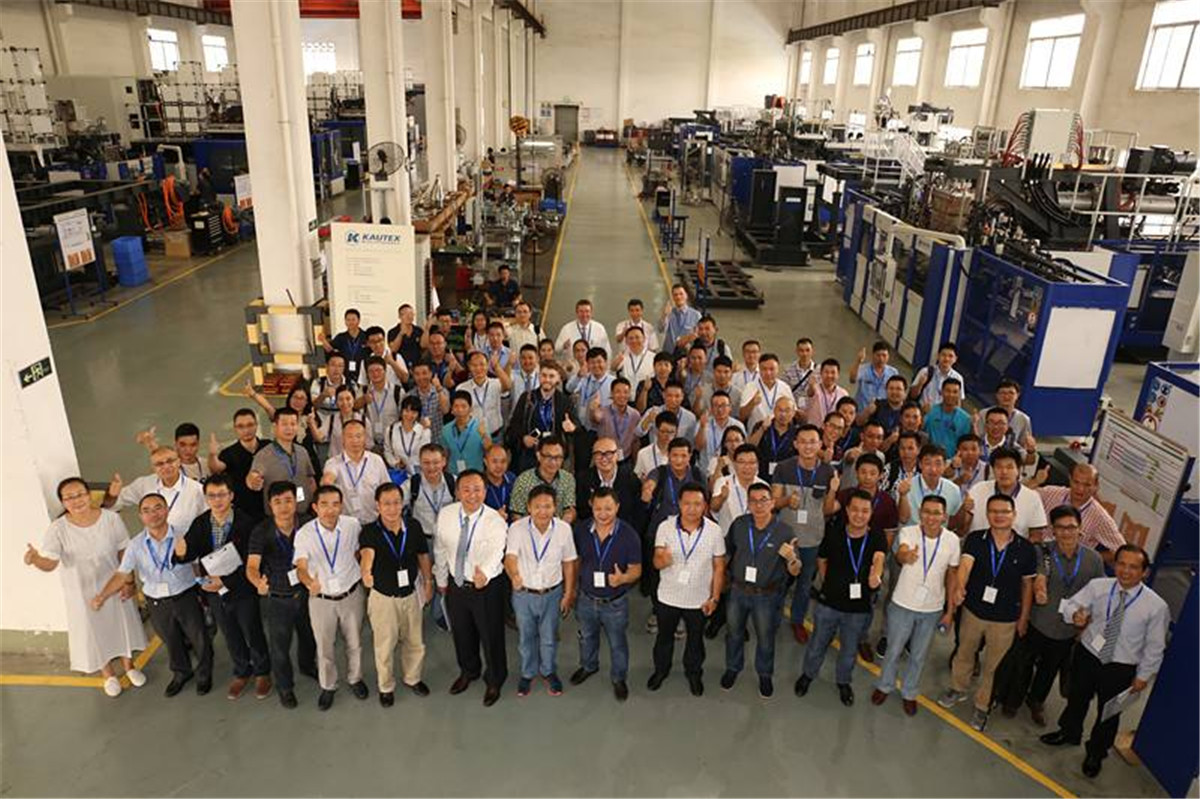
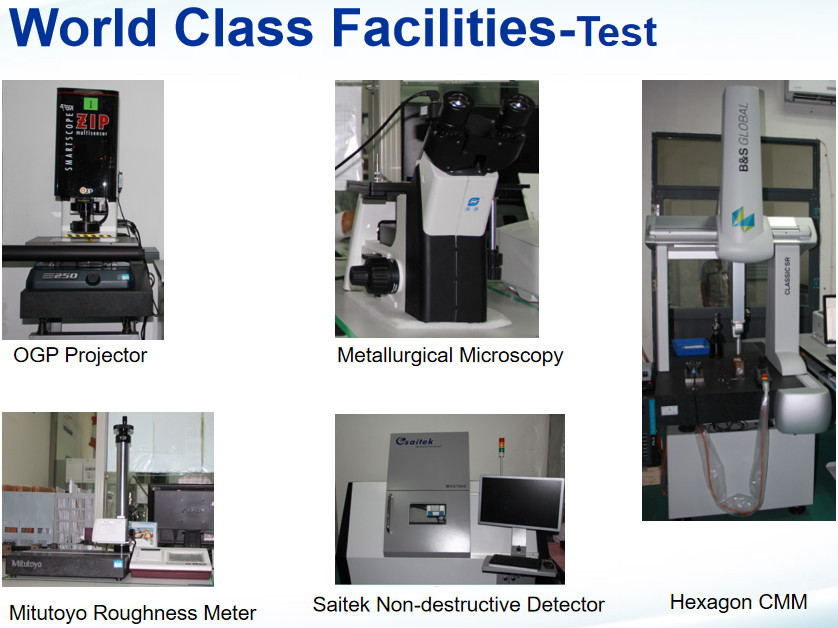
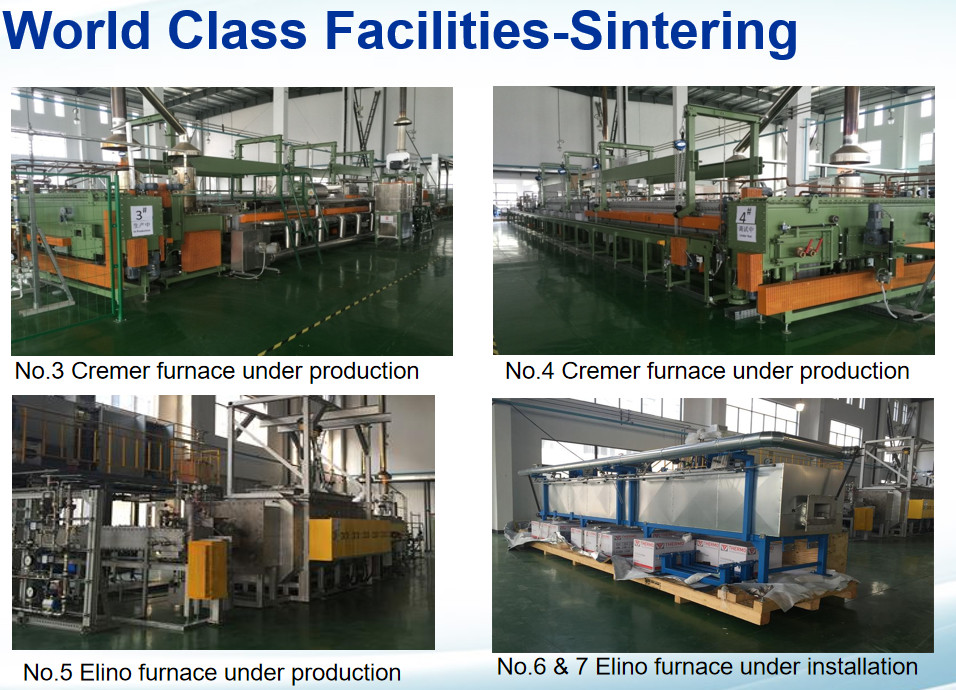
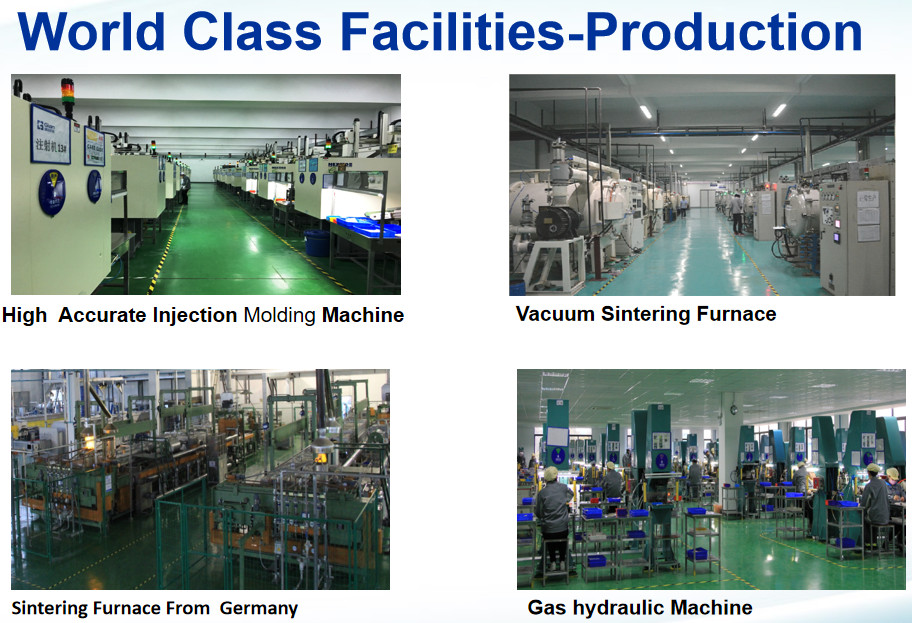
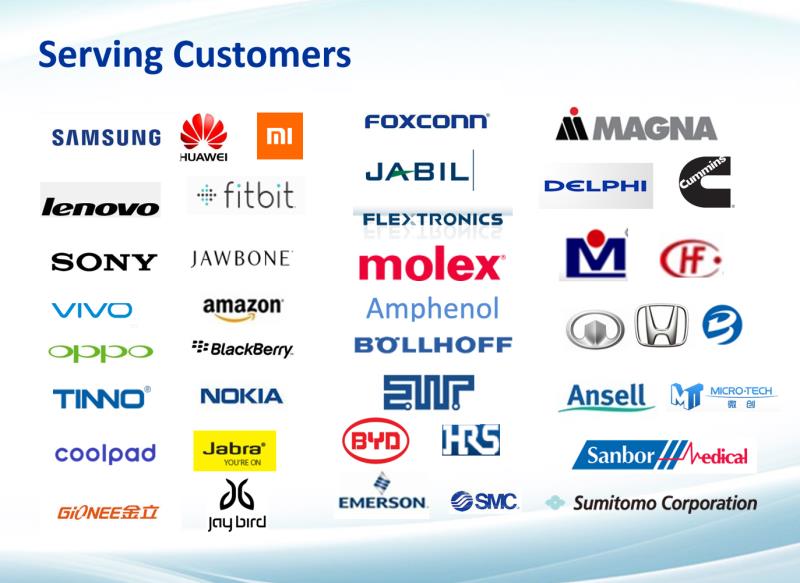