Powder metallurgy?
Powder metallurgy injection molding was born in California, USA in 1973, referred to as MIM. It is a new type of powder metallurgy molding technology invented by combining plastic injection molding technology with the field of powder metallurgy.Powder metallurgy is close to the injection molding process with powder metallurgy technology, first the solid powder and organic binder mixing together, through 150 degrees high temperature heating plasticizing, injection mold cavity with injection molding equipment, again is solidified, then use the method of thermal decomposition of binder removal from the billet, the last as powder metallurgy, precision by sintering parts. Powder metallurgy compaction molding is to use powder to fill the mold by gravity, through the machine pressure extrusion molding.In practical industrial applications is the most widely used one, cold closed steel die pressing, cold isostatic pressure, hot isostatic pressure, temperature pressure are pressing molding.However, due to the only up and down two-way pressing, some complex structural parts can not be produced, or can only be made into blank. The use of powder metal technology bypasses the need to produce the resulting products by metal removal processes, thereby reducing manufacturing costs. As a leading powdered component manufacturer, we provides a wide variety of powdered and sintered metal gears for several applications in multiple industries. The manufacturing of sintered metal gears can present many challenges for conventional manufacturers. Gear geometries are inherently complex, often requiring time-consuming secondary machining processes – adding cost to the bottom lime. It is in this realm where powder metallurgy excels. Through the use of precision tooling, high tonnage compaction pressure, and sintering, gears may be manufactured with the powdered metal (PM) method, to near-net-shape or even net-shape, requiring little or no machining, and at cycle times considerably faster than machining. Benefits of Using PM in Gear Manufacturing Utilizing PM for gear manufacturing provides many benefits including tight tolerances, quiet running PM gears, and the capacity for higher volumes. A key benefit of using powdered metal for gear manufacturing is the cost-effectiveness. The ability to produce multilevel gears combined with internal configurations and tight tolerance components eliminate or reduce the need for additional operations. All together results in time and money saved for your application. With little to no waste, powdered metal is a green process due to its low energy usage and minimal scrap, making it more economical than standard machining or casting. Material selection for powdered metal gears allows for optimization of the component’s performance for its intended application with little variation in the manufacturing process.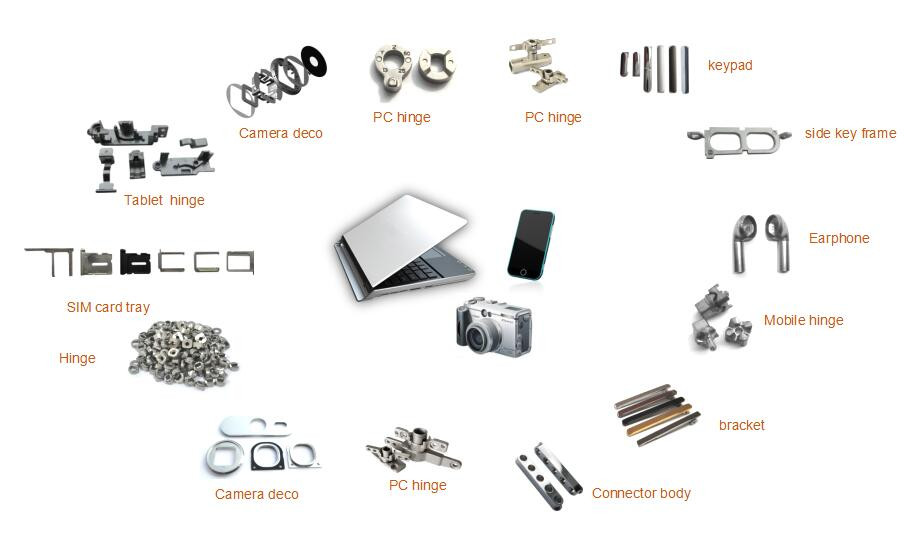
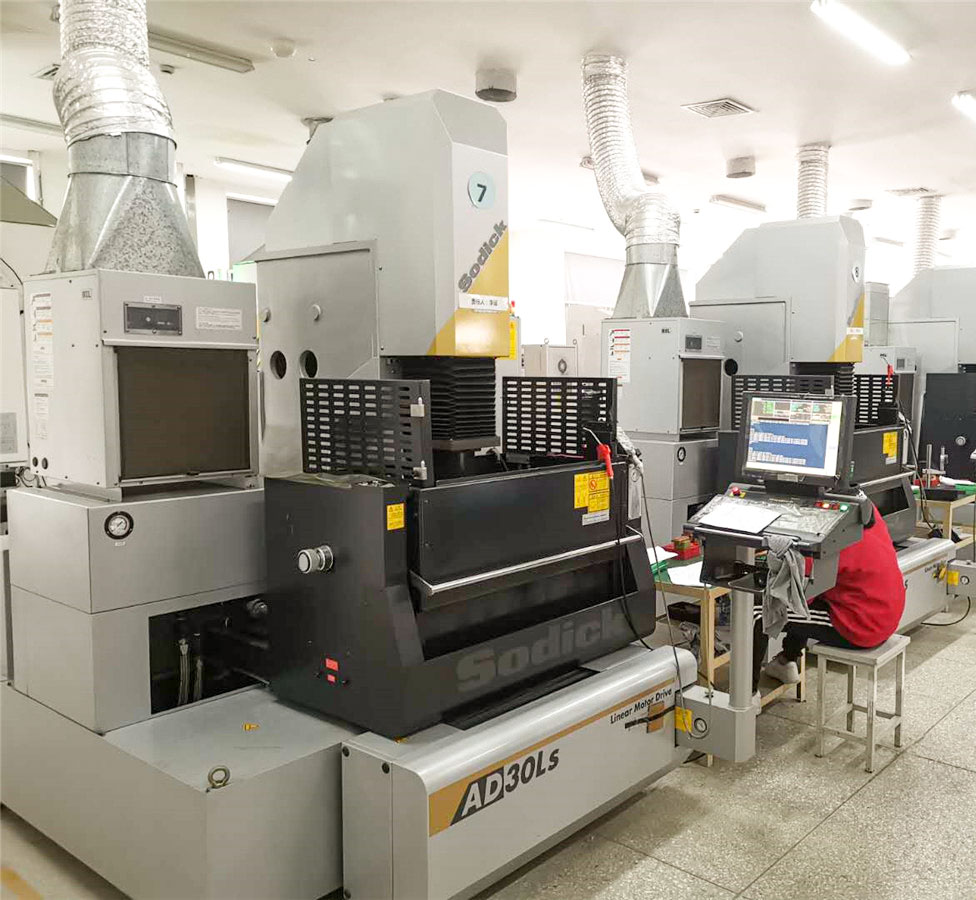
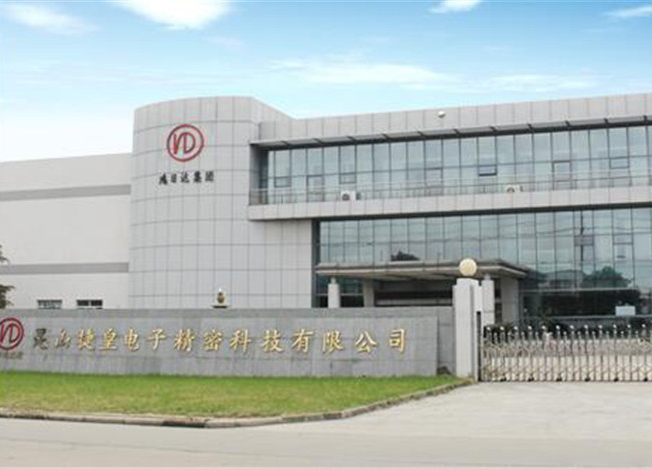
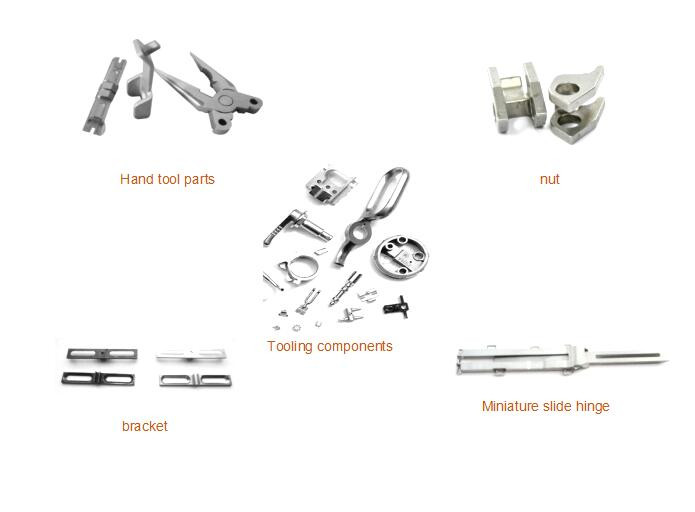
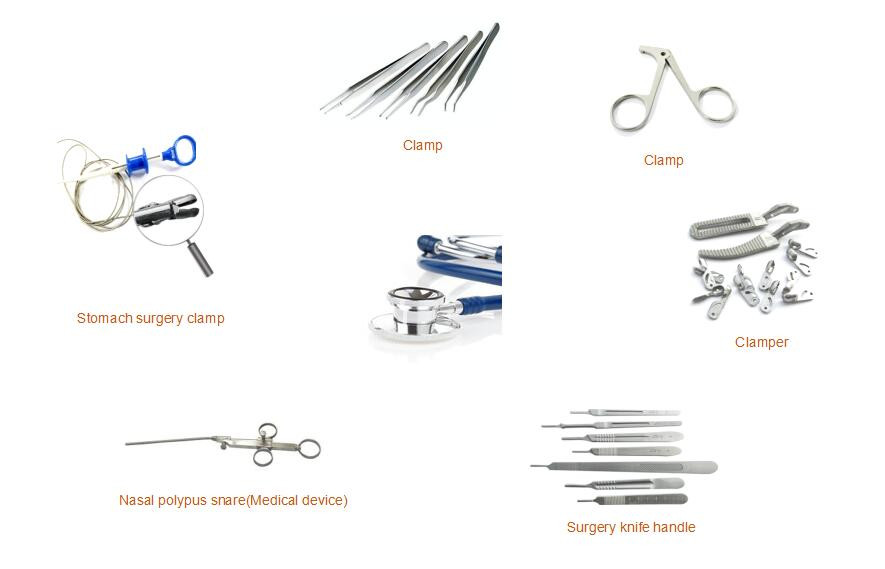
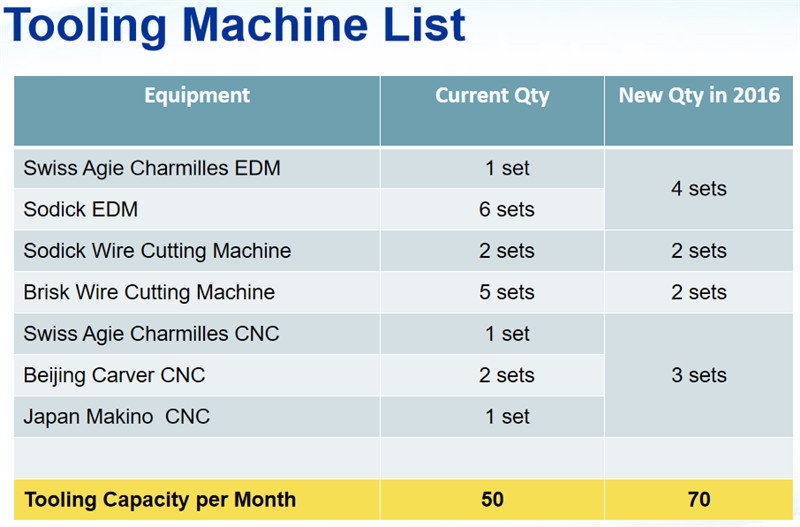

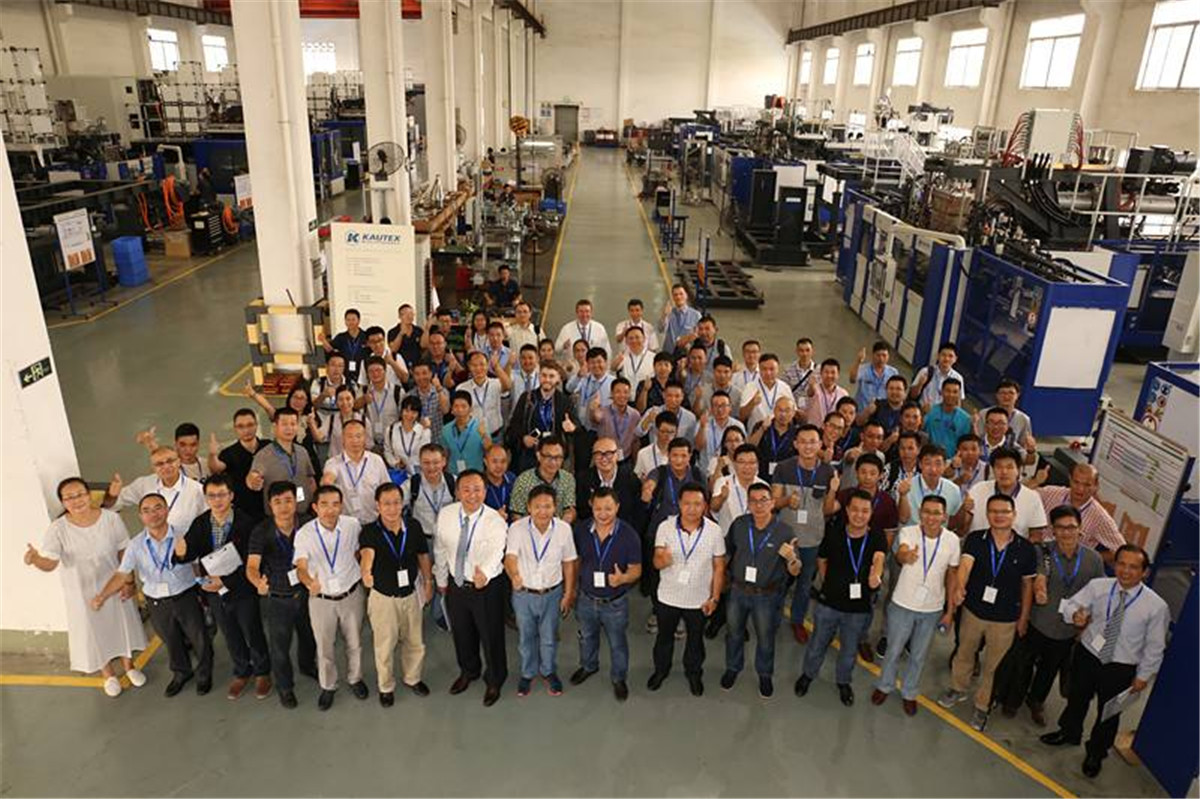
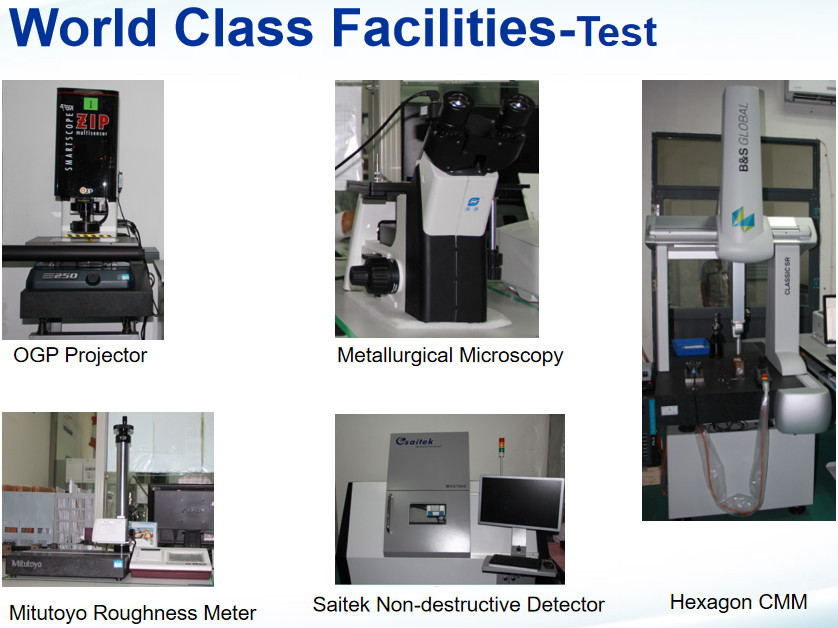
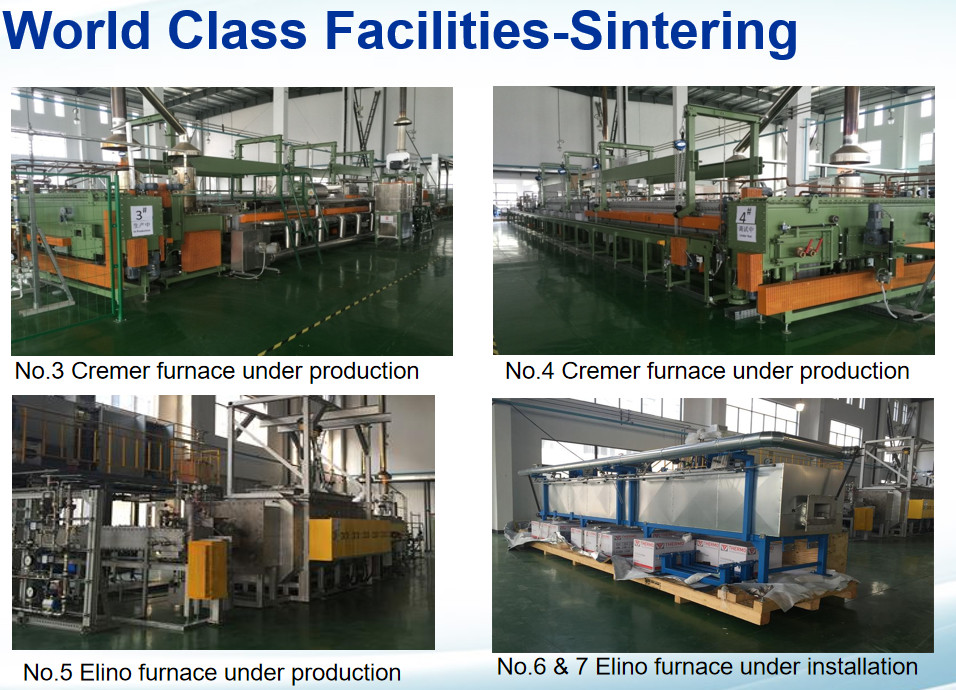
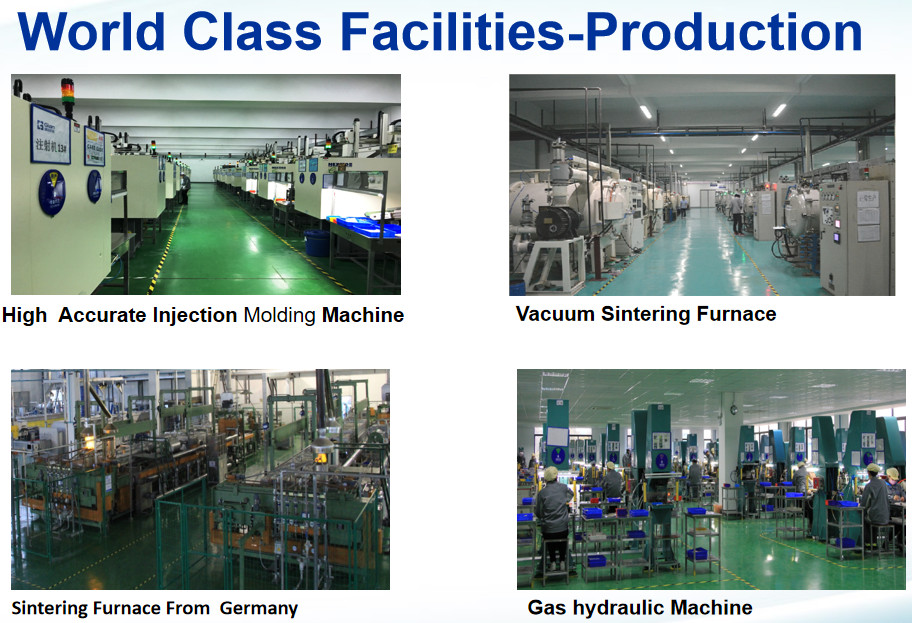
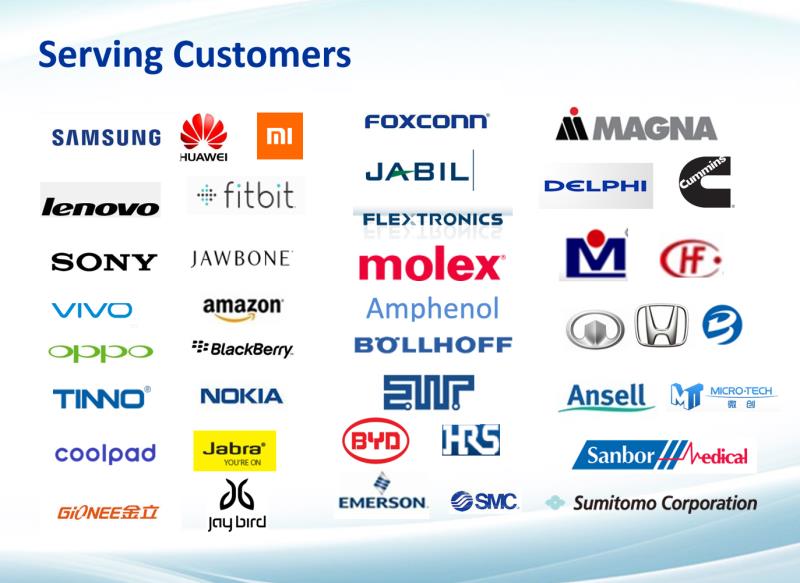