Powder metallurgy is the process of using metal powders to create solid parts through compacting and sintering. The process begins with the preparation of metal powders through primarily mechanical means, while chemical methods may also be employed. The powders are then mixed with a suitable binder before being pressed into the desired shape using high pressure. This ensures that the powder particles are securely held together, preparing them for the next step which is heating in a furnace. As the metal is heated, the powdered particles start to fuse, resulting in the creation of a solid part of high density, and if done correctly, with a uniform microstructure throughout.
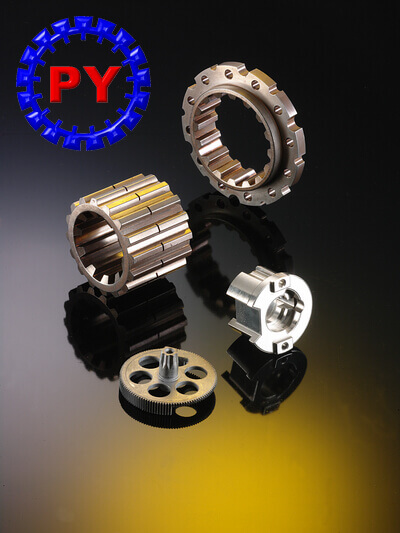
The resulting parts are strong, durable, and exhibit unique properties that match those of cast materials. Advancements in the process have allowed powders to be engineered to offer a range of properties based on the specific requirements of the parts being produced. Through the powder metallurgy process, virtually any metal, including the rare and expensive types, can be molded, offering designers significant freedom to create any shape or design that meets their needs.
Metal injection molding (MIM), on the other hand, comprises two primary stages: injection molding and debinding/sintering. The first step involves the production of feedstock, which consists of fine metal powders and a small binder. The feedstock is then injected into a mold similar to that used for plastic molding. Here, the molding ensures that the part is produced to the precise requirements of the part's design.
The next step involves the removal of the binder used in the first stage. The process is known as debinding and is typically done through solvent washing. This step removes the binder without compromising the desired microstructure of the part. After debinding, the part is subjected to a high-temperature treatment to sinter the metal powders. This ensures that the powder particles fuse together, resulting in a high-density part with a uniform cross-section.
Metal injection molding offers greater design freedom and flexibility than traditional injection molding, and it has the advantages of powder metallurgy in producing custom metal parts with high-precision, complex shapes, and intricate features. MIM uses low-cost raw materials to produce high-value, intricate components in a process that is highly scalable and efficient. Furthermore, it can create parts that are difficult or impossible to make with other techniques or cost-prohibitive, and owing to its precision capabilities, it is popular across a diverse range of industries.
In conclusion, metal sintering has proven to be an invaluable tool in the production of intricate metal parts with high precision. Whether via the powder metallurgy process or metal injection molding, designers have access to a range of techniques that allow them to create precision parts of almost any shape imaginable. As technology advances, so too will the range of applications for sintered metal parts, ensuring that the process remains an important part of many industries.